The smelt
Usually, equal weights of ore and charcoal are added, 1kg of each per charge. Prior to charging, the charcoal is broken into pieces not larger than about 20mm, and the roasted ore broken to a maximum size of about 10mm. Both are sieved to remove particles less than about 1mm in size to ensure free passage of the gases through the furnace bed.
The smelt proceeds with a fresh charge being added every 10 to 15 minutes, depending on the airflow rate, to keep the furnace full. Temperatures and the blowing rate are carefully monitored and the blowing rate adjusted if necessary to maintain the required temperature at the lower thermocouple. Typically, this is around 1050°C, but temperatures between 950°C to 1125°C have all successfully yielded blooms.
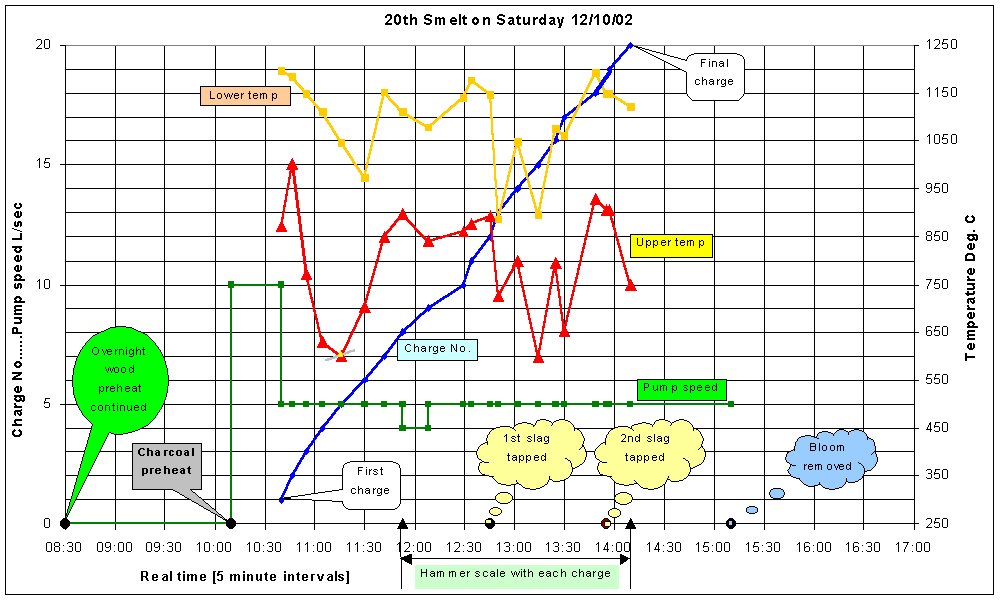
Reduction of the ore with charcoal can, in theory, start at temperatures above about 680°C, but it only reaches an appreciable rate at temperatures above about 900°C. The rate of reduction increases as the ore descends through the furnace because the temperature increases towards the tuyere. The iron never melts, but much of the iron in the ore combines with the non-iron bearing minerals in the ore to form a molten slag. The aim is to produce a low melting point slag that will carry particles of solid iron through the furnace where they agglomerate to form a lump of iron called the bloom. This adheres to the wall just below the tuyere. The lowest melting point constituent of the slag melts at 1070°C, but, depending on the slag composition, higher temperatures are generally required to form a fluid slag. We aim for a slag composition which melts at about 1178°C, which corresponds to a composition close to 2FeO.SiO2, known as Fayalite (an iron rich olivine). The temperature in the furnace exceeds this temperature in a region around the tuyere and so a molten slag forms.
The slag from the furnace is rich in iron oxide, sometimes with over 50% FeO either as FeO (known as wustite), or combined with silica (Fayalite 2FeO.SiO2). It is postulated that the high FeO content in the slag and the fact that the slag is molten plays an important part in the formation of the iron bloom as the FeO reacts with carbon dissolved in the iron particles thereby reducing their carbon content (decarburisation) and at the same time produces more iron which ‘cements’ together the particles of iron to form a dense bloom.
The reaction proposed is: FeO(in slag) + C(in bloom) = Fe + CO
The CO so formed travels up the furnace where, along with the CO produced by the burning charcoal, it reduces more ore.
Another theory (1), however, is that fluid slag is important in preventing the carburisation of the iron surface by stopping the CO-rich gas formed in the highest temperature region of the furnace coming into contact with the bloom. It is argued that this also prevents the iron melting as its melting point decreases as the carbon content increases. For example, cast iron with a carbon content of 4.3% has the lowest melting point at 1130°C, a temperature easily exceeded in a bloomery furnace, but pure iron has a melting point of 1550°C. The carbon content of a bloom does not usually exceed 0.8%C, a composition which would start to melt at 1475°C. We have observed a carbon content as high as this in some regions of the surface, but the carbon content inside the bloom is generally much lower, typically a few points of a percent.
Periodically, slag is tapped from the furnace to prevent too much accumulating which may block the air flow through the tuyere and also to prevent the thickening of the slag due to composition change which prevents its free flow through the bloom, a phenomenon we have observed. The first slag tapping is normally required after about three hours of smelting. Sometimes, before this time, it is necessary to disconnect the air supply and force a rod down the tuyere to clear it of slag. The slag is tapped by unblocking the slag arch and prodding the mass of slag which has accumulated to break its cooler ‘skin’. Molten slag then usually flows, typically 500g accumulating outside and on the bottom of the furnace. The slag-tapping arch is then resealed.
The smelt proceeds for about five hours, during which time typically 15 – 20kg each of ore and charcoal are added. The final charge is charcoal only to maintain the reducing conditions while the last ore charged works its way down the furnace.
In recent experiments, we have added an additional 100g (10% of the ore charge) of hammer scale to each charge from half way through the smelt. Hammer scale is the ‘waste’ produced as the bloom is hammered during forging and consists of 100% iron oxides. Its addition part way through the smelt is intended to dilute the silica content of the slag in an attempt to produce more of the lower melting point fayalite. The resulting compositions of the slags are the closest we have produced to Roman slags. We speculate that recycling such a rich source of iron would have been practised in Roman times as such scale would have been readily available from the smithing operation.
(1) Influence of the Ore Smelting course on the slag microstructures at Early Ironmaking, usable as Identification Basis for the Furnace Process Employed, Stig Blomgren & Erik Tholander, Scan. Journ. Metallurgy 15 (1986) pp.151-160
Continue: Summary The Ore Ore Preparation The Furnace The Smelt The Bloom Comparison with Ancient Slags Limitations in Analysis References Pictures